The playability of a Taylor guitar neck is legendary. It starts with a comfortably slim, hand-friendly neck profile, but there’s actually a lot more that goes into creating the optimal relationship between the guitar neck and guitar body to deliver the best possible playing experience.
Our patented neck design, introduced in 1999, was a breakthrough innovation that changed the way an acoustic guitar neck joins the body. In fact, it was widely recognized by guitar experts as one of the most significant improvements to acoustic guitar design in the 20th Century. The design not only allows the neck angle to be set with pitch-perfect accuracy, it also allows for easy micro-adjustability over time, allowing the guitar’s playability to be maintained for a lifetime. It also makes the neck more stable in the face of humidity fluctuation.
Here’s a closer look at the key elements of our patented neck design and how they work together to enhance the Taylor playing experience.
Three-Piece Neck
Rather than being produced as a single piece of wood, our necks incorporate a three-piece design, consisting of the main neck shaft, the peghead and the heel. (The pieces are all cut from the same wood blank to maintain consistent density, wood grain and coloration.) The benefits of the three-piece design are several-fold: It combines structural improvements (see “Scarf-Jointed Peghead” below) with greater computer-controlled milling capability, which allows us to make a straighter, more stable neck. The three-piece design also reduces wood waste (see “Wood Conservation” below).
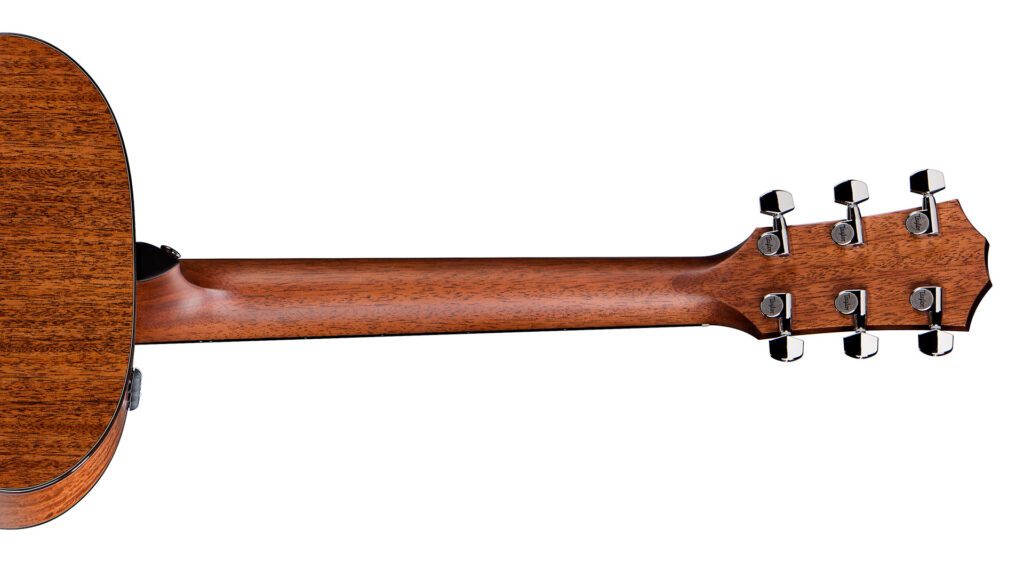
Scarf-Jointed Peghead
Part of the three-piece neck design, this glue joint where the angled headstock meets the neck shaft more than doubles the strength of the neck in this area, giving it more resilience. On a single-piece neck, this is typically a structurally vulnerable area, often absorbing the brunt of the impact if a guitar is knocked over.
Wood Conservation
Adopting our three-piece design approach allowed us to change the cutting specifications for our neck wood (typically mahogany) to increase the yield from each tree harvested. Rather than cutting traditional rectangular 3×4-inch neck blank dimensions, Bob Taylor changed our specification to cutting 4x4s. This ensures the proper grain orientation every time — the wood can’t be cut wrong because of its square dimensions — and as a result, roughly doubled the wood yield from each tree. It’s a good example of our ability to re-engineer a process not only to improve the guitar’s performance but to reduce material waste.
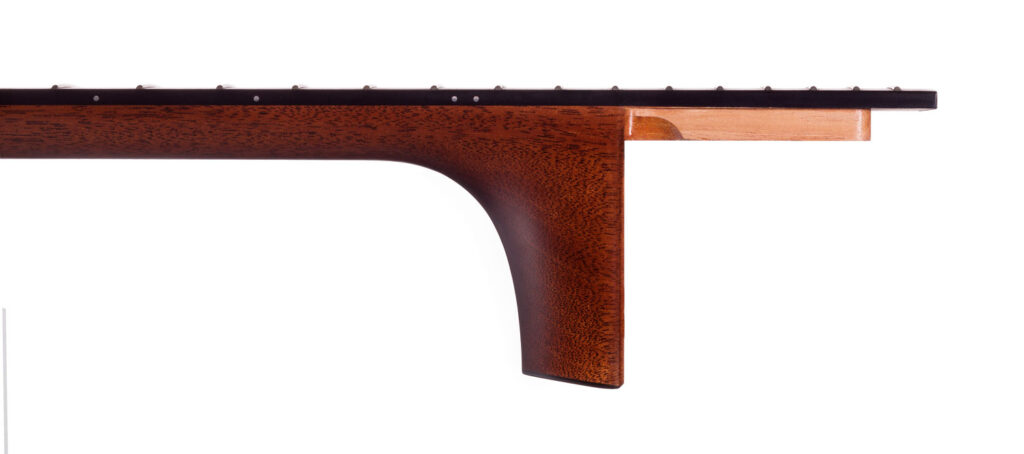
Neck Paddle
This part of the neck, which extends beyond the heel, supports the fretboard extension (the part of the fretboard that runs from the edge of the body to the soundhole) and provides increased stability along with better transfer of tone between the body and neck. The paddle will be inset into a dual-pocketed neck block built into the guitar body.
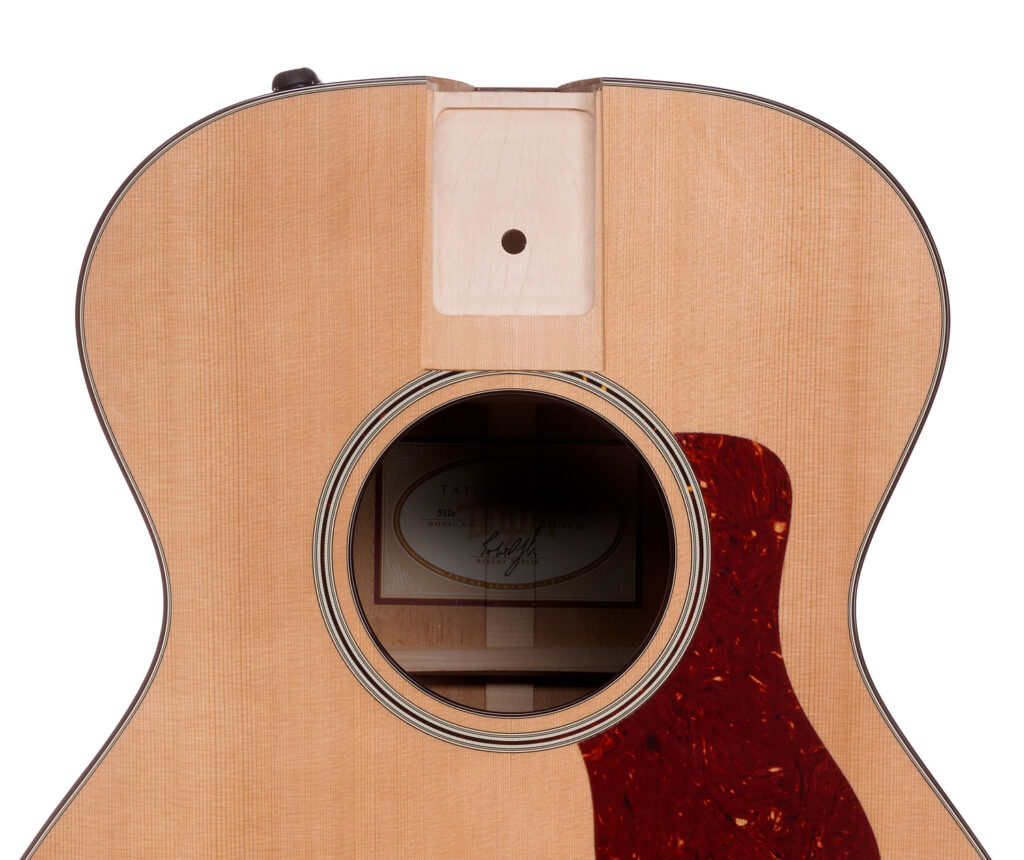
Dual-Pocketed Neck Block
Two pockets are precision-routed into a neck block built into the guitar body using a CNC mill. The pockets are cut perpendicular to each other. A pair of neck angle spacers will be inserted into the pockets to set the precise neck angle, and then the neck will be inset into the pockets and bolted securely in place. One of the benefits of this approach is that the fretboard extension does not need to be glued to the guitar top to secure it, which helps make the neck more stable in the face of humidity fluctuation.
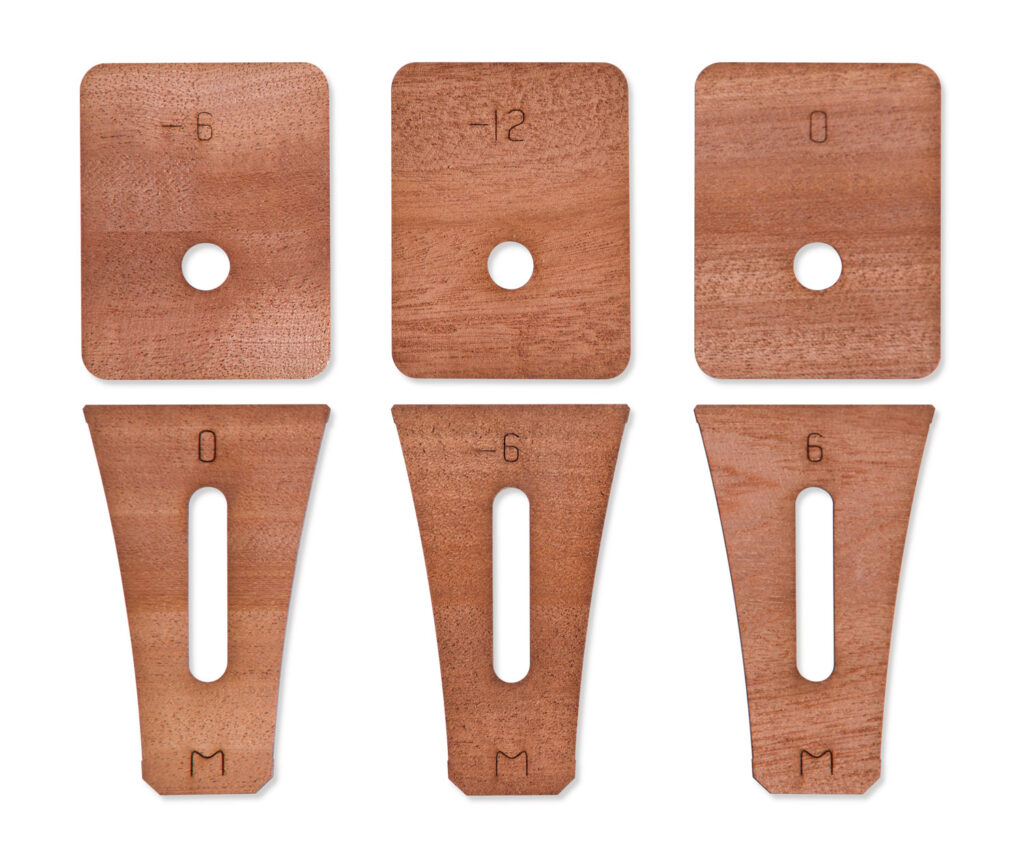
Neck Angle Spacers
Laser-cut and milled in varying increments of .002 inch, these precision spacers, or shims, form the basis of setting the perfect neck angle to optimize the feel and sound of the guitar. The spacers are inset (without glue) into the two pockets where the neck will meet the body and can be changed easily to micro-calibrate the neck angle both during the final assembly process at the Taylor factory department and throughout the guitar’s life.
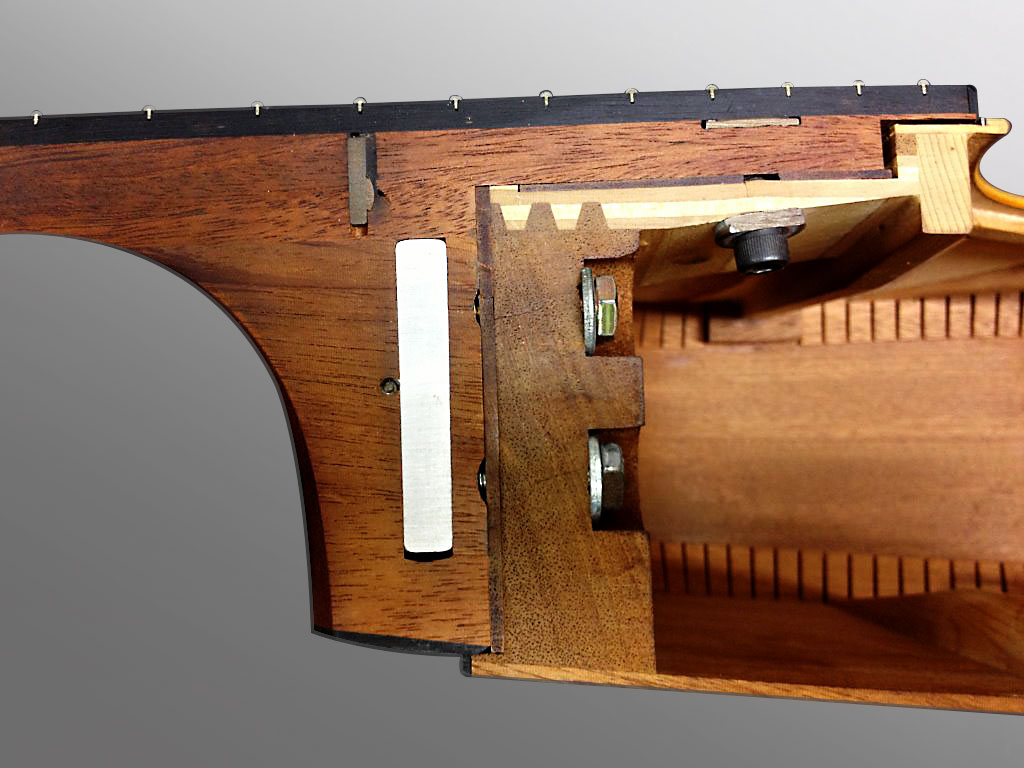
Glue-Free Assembly
The glueless, three-bolt assembly ensures a secure wood-to-wood surface connection between the neck and body, which enables a strong transfer of sound. (Glue can inhibit tonal transfer.) The design also makes it easy to remove the neck for service at any time — there’s no glue joint that needs to be steam-treated to loosen for removal.
Bridge/Saddle
Like the neck and body, these are CNC-milled for accurate and consistent dimensions. This contributes to our ability to set the precise body geometry on all guitars.