Ever heard the term “urban forest”? It refers to the planned and managed tree canopies that form the green infrastructure of communities, including the public landscaping of neighborhoods, metropolitan areas, and larger regions. Think of the trees on your street, along highways, at schools, shopping centers, parks and other public spaces. They’re planted with a purpose and provide numerous benefits: They absorb carbon dioxide, filter pollution, provide shade and windbreaks, absorb noise, and create habitat for birds and other wildlife, not to mention their many other community-enhancing aesthetic and social virtues.
These green ecosystems are managed by municipalities and public agencies, who are responsible for overseeing the planting and maintenance of trees, along with their removal due to weather or disease damage, public safety concerns, disruptive root systems, and simply reaching the end of their life cycle. Often, municipalities contract with an arborist to provide these services.
Ever wonder what happens to trees when they need to be removed? Historically speaking, not much. Traditionally, they’ve been disposed of, often in landfills, at taxpayer expense. To offset some of those disposal costs, many municipalities turn a portion of that wood into low-value products like firewood or mulch. In recent years, some enterprising small businesses have been turning urban wood into higher-value products such as slabs, lumber and other artisanal goods.
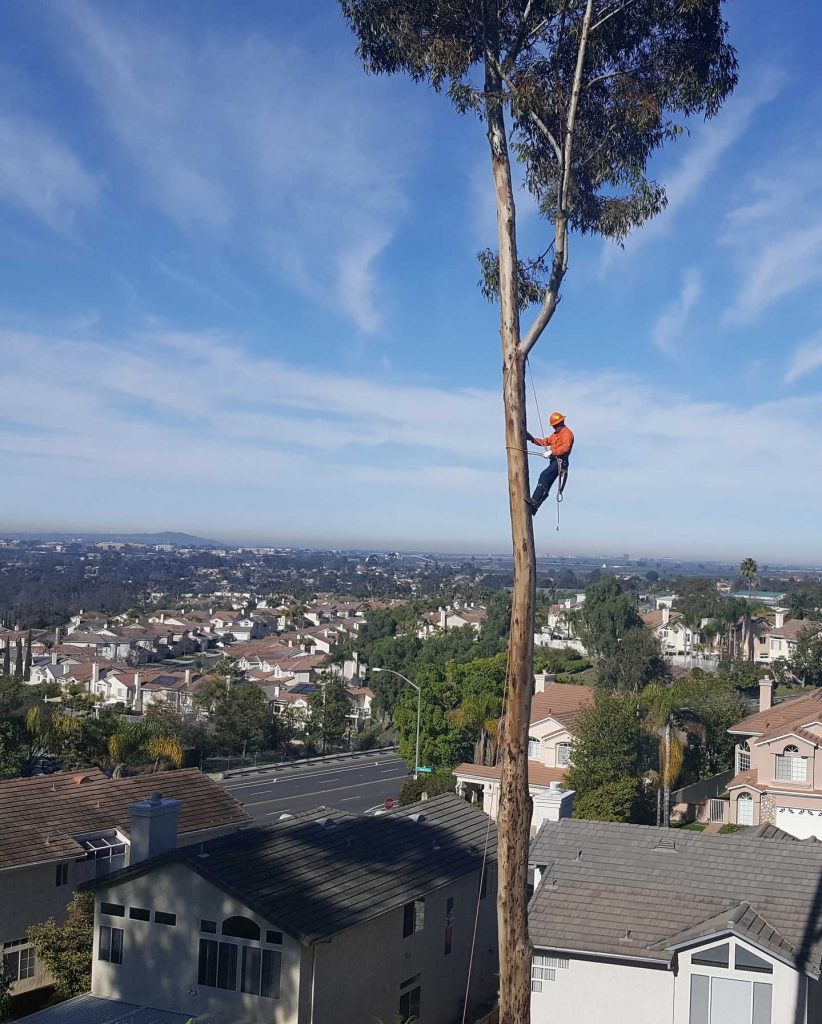
A couple of years ago, Taylor Guitars co-founder Bob Taylor, our Director of Natural Resource Sustainability, Scott Paul, and resident master builder Andy Powers began to explore the idea of making guitars from some of this available urban wood as another expression of our commitment to responsible sourcing practices. The prospect of sourcing wood locally, from our extended backyard of Southern California, was especially appealing. As Andy points out, historically, makers of string instruments used materials that were locally available. Over time, as the ability to transport logs and lumber around the world improved, instrument makers began to embrace other exotic and musically appealing tonewoods from far-flung parts of the globe.
“In a way, instrument makers became like spice traders, introducing new ingredients into familiar recipes,” Andy says.
Over the past century, the increasing global demand for certain wood species, across a variety of industries, has strained forest ecosystems in certain parts of the world. Our awareness of this reality led us to launch several initiatives to help preserve the future of some of those forest resources we rely on in other regions, such as planting ebony trees as part of our Ebony Project in Cameroon and helping to restore native Hawaiian forests and plant koa trees in Hawaii. By also sourcing urban woods for guitars, we might be able to ease the stress on forests elsewhere, while also helping to create a circular economy around this underused resource closer to home.
Partnering with West Coast Arborists
In our effort to learn more about urban forest management, we reached out to our local arborist, a company called West Coast Arborists, Inc. (WCA). It turns out that they’re not merely a small local company. Based in Anaheim, California (about 100 miles from the Taylor factory), they’re an established business (founded in 1972) with about 1,000 employees, and they provide tree maintenance and management services to more than 300 municipalities and public agencies across California and Arizona.
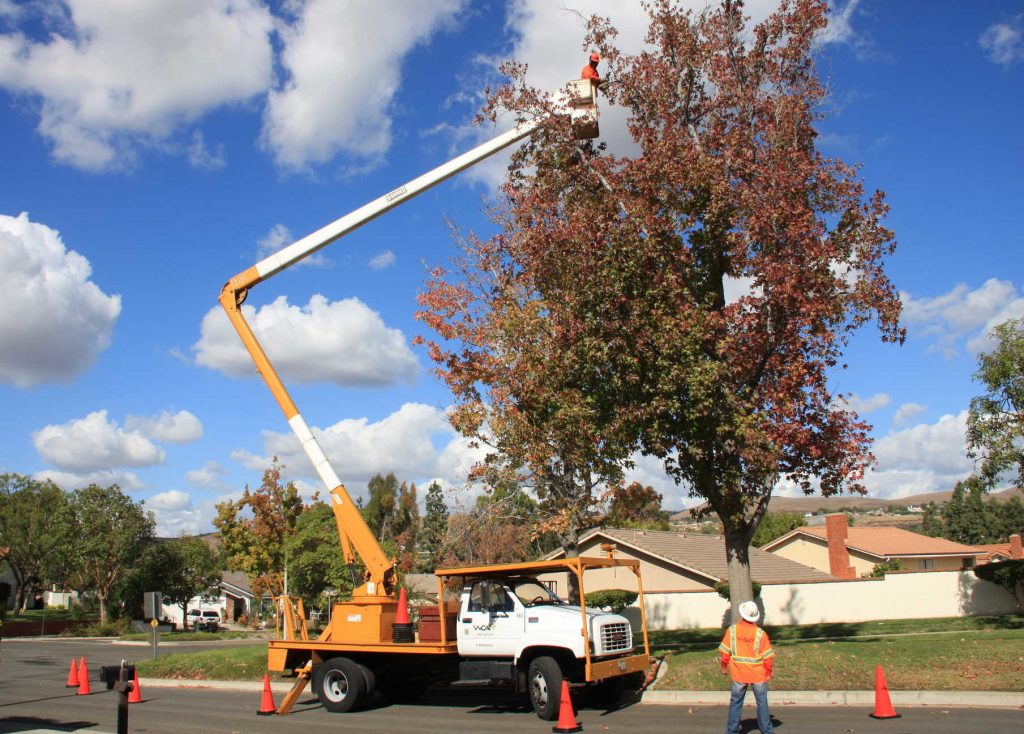
The company’s ability to manage tree inventories across the regions they service is remarkably technologically advanced, thanks to proprietary software that incorporates GPS tracking and other data integration. Currently, they have more than 10 million tree sites inventoried in their computer database, and they have a mobile app that their network of arborists and their clients can use.
“We were blown away by the foresight and the infrastructure they’ve developed over the years,” Andy says. “What they’ve accomplished is really impressive.”
Each year, WCA plants between 18,000 to 20,000 new trees. They also remove trees when requested by a city, taking them to their strategically located log yards across the state to facilitate disposal. To offset rising disposal costs and develop socially responsible market alternatives to keep trees out of landfills, WCA launched a pilot urban wood recycling initiative dubbed Street Tree Revival with the California Department of Forestry and Fire Protection (CDF). It has since grown into a larger enterprise that supplies both live edge and dimensional lumber.
Taylor’s Urban Ash™ Guitar
The question for Taylor was whether any of the tree species from WCA’s log yard inventory were musical-instrument-grade tonewoods, and whether there would be a reliable enough supply with consistent quality standards to support using the wood for a dedicated model in our guitar line rather than simply a limited-edition offering.
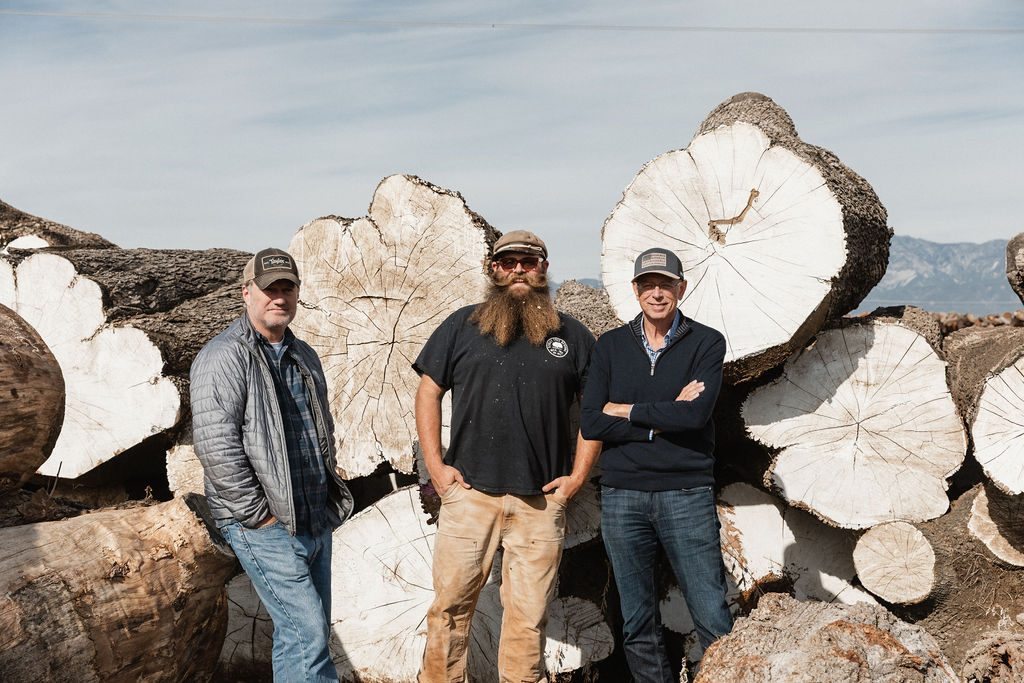
A Taylor group including Andy and Bob Taylor visited WCA’s sort yard in Ontario, California, where they found several species that excited them. After cutting and drying some of the wood and later building prototype guitars, Andy chose a species of ash known locally as Shamel ash.
“Its ancestors are Mexican evergreen ash,” he says. “It’s known as tropical ash in some places, and was propagated 60-70 years ago because it was considered well-suited for Southern California’s climate. In addition to the deliberate planting, these trees proved prolific and spread throughout Riverside, the Inland Empire, and the LA basin, where they often grow very large.”
Here at Taylor, we’re calling it Urban Ash to help draw more attention to the idea of using urban woods. To Andy, its characteristics make it a strong contender as a high-grade guitar wood of the future.
“This particular species happens to be great mix of the right weight, density, dimensional stability and drying attributes, and responds well to sawing, sanding and finishing,” Andy says.
He was equally excited about the tonal properties of the prototype guitars he built using the wood for the back and sides.
“In almost every physical way I can measure it, it’s reminiscent of good mahogany,” he says. “It tends to be relatively consistent throughout the board. Compared to other ash species used for electric guitars, it’s heavier, denser and more resonant than the ‘swamp’ ash loved by electric guitar makers, but not nearly as heavy or tough as the Northern baseball-bat ash.”
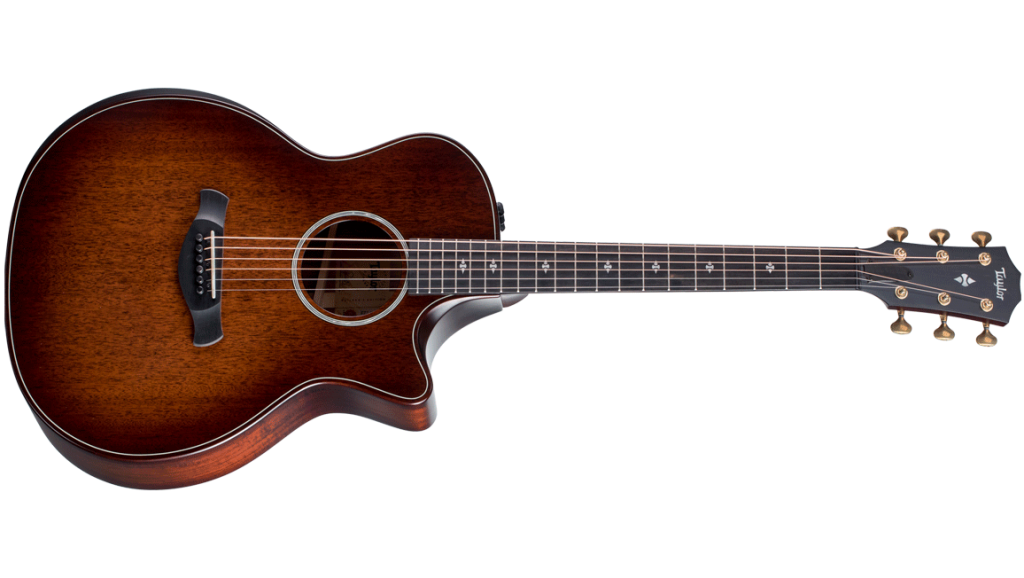
Andy chose to introduce Urban Ash on one of Taylor’s premium-class guitars, the Builder’s Edition 324ce. The decision underscores his passion both for the performance virtues of the urban wood itself and the prospect of Taylor working with West Coast Arborists to shape a new urban forest sourcing model using locally available resources.
“An initiative like this is another example of our commitment toward better environmental stewardship,” he says. “Sure, conservation and replanting are critical aspects in our quest toward a better forest future. In addition, we can take a fresh look around us and adapt designs to use what is currently available and build with it in a responsible way.”
Though Taylor is still in the early stages of working with WCA, the two companies have a lot in common in terms of their parallel histories in Southern California, their innovative mindsets, and a shared desire to use business as a driver of environmental stewardship. Because of WCA’s relationships with hundreds of municipalities, there is great potential to build additional partnerships with public agencies and bring more infrastructure and more resources to urban forest management, including re-greening projects in communities throughout our region and beyond.
To learn more about urban forests, see Scott Paul’s column in the latest issue of our publication, Wood&Steel.